Влияние некоторых составляющих асфальтобетонной технологии на долговременную ровность дорожных покрытий
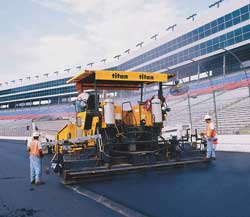
Дорожными нормативами большинства стран мира предусмотрены определенные требования к значениям показателей ровности покрытий автомобильных дорог, несоблюдение которых может привести к серьезным проблемам и последствиям, особенно в части обеспечения безопасности дорожного движения.
Главными экспертами этого важнейшего качества дороги, испытывающими непосредственно на себе все достоинства и недостатки ровного или «корявого» покрытия, являются в первую очередь водители и пассажиры автомобильного транспорта, затем, конечно же, автомобиль и сама дорога, быстро выходящие из строя при своих перегрузках на неровных покрытиях и требующие немалых затрат на свои ремонты.
Поэтому в России нормативные межремонтные сроки службы дорожных покрытий устанавливают по моменту достижения ими предельно допускаемого эксплуатационного состояния, оцениваемого их ровностью. Значения последней взаимоувязаны с безопасностью движения и проектным уровнем надежности дорожной конструкции в целом. Например, при уровне надежности 0,95 (дорога I категории) неровности на покрытии по толчкомеру ТХК-2 на автомобиле УАЗ не должны быть больше 80–100 см/км, а при надежности 0,90 – не более 170 см/км (III категория). В противном случае покрытие должно быть поставлено на ремонт.
На рис. 1 показана расчетная схема и аналитические зависимости для определения силы динамического воздействия колеса автомобиля на поверхность покрытия при наличии на ней одной из часто встречаемых неровностей в виде впадины, выбоины или ямы. Уместно заметить, что такие неровности глубиной до 6–10 мм (в среднем 8 мм) вполне легально могут быть на покрытиях российских дорог, ибо СНиП 3.06.03-85 допускает их, но в количестве не более 10 %.
![]() |
Рис. 1. Схема воздействия колеса автомобиля на дорожное покрытие в момент прохождения выбоины. |
Грузовой автомобиль при весе заднего моста с колесами всего около 2–3 % от его общего веса с грузом при проезде на скорости 60 км/ч этой неровности шириной или диаметром 0,5 м воздействует на покрытие с максимальной динамической силой, превосходящей статическую нагрузку на эти колеса примерно в 1,5 раза (коэффициент динамичности Kd = 1,45). При неровностях большей глубины или высоты эта сила возрастет еще значительнее.
Асфальтобетонные покрытия, как правило, долго не выдерживают таких многократно повторяющихся перегрузок, так как нормативное значение коэффициента динамичности, принимаемое при прочностных расчетах дорожной одежды, не превышает 1,15. Вот почему в местах появления различных дефектов, деформаций и неровностей на покрытии размеры последних очень быстро разрастаются, еще больше и опасно ухудшая общее состояние дороги по ровности.
Отсюда знакомая уже многим дорожным подрядчикам полезная заповедь – хочешь быть конкурентоспособным и привлекательным заказчику, строй и сдавай дороги одновременно прочными и ровными и на этой основе повышай гарантийные сроки своих объектов.
Фирма ВАД, видимо, одной из первых среди подрядчиков новой России не только поняла глубокий технологический, экономический и, быть может, даже философский смысл этой заповеди, но и стала реально воплощать ее на практике, доведя контрактные и фактические гарантийные сроки многих своих объектов до 7 лет, своеобразно догнав передовые дорожные Европу и Америку, где иногда тоже дают подобные сроки гарантий.
Этого удалось добиться, главным образом, за счет постоянной заботы о повышении качества и равномерности уплотнения земляного полотна, щебеночных оснований и асфальтобетонных покрытий, а также непрерывного поиска и применения наиболее совершенных и результативных технологических приемов и средств укладки этих материалов более ровными слоями.
Внедрение новой, а точнее, усовершенствованной технологии (собственная разработка ВАДа) укатки асфальтобетона комбинацией вибрационных и статических катков позволило не только поднять средний уровень получаемой плотности, но и добиться надежной и устойчивой ее реализации на всех без исключения объектах 2004 г. Теперь минимально требуемый по СНиП коэффициент уплотнения асфальтобетона (для щебенистого 0,99, или 99 %), как правило, не превышает 5–10 % в общем количестве тестовых кернов из покрытия, а остальные достигают значений 1,0–1,02 (100–102 %). Раньше все было наоборот.
Ровности устраиваемых покрытий ЗАО «ВАД» всегда уделяло особое внимание. Поэтому в арсенале используемых новинок в свое время появились скоростные автосамосвалы Volvo (Швеция), способные быстро и без существенных потерь тепла доставлять горячую асфальтобетонную смесь на расстояние до 150 км; специальные перегрузчики Shuttle Buggy фирмы Roadtec (США), бесконтактно подающие смесь из автосамосвала в бункер асфальтоукладчика с одновременным устранением ее гранулометрической и температурной сегрегации; длинномерные (18–24 м) двойные лыжи по типу французской и др.
Если прежде уровень значений показателя ровности покрытия в пределах 20–30 см/км по толчкомеру ТХК-2 (УАЗ) считался очень хорошим, то сегодня такой результат воспринимается уже как обычный или даже недостаточный, потому что на ряде объектов он улучшен до уровня 10–20 см/км. И не только по толчкомеру ТХК-2 (УАЗ).
Ученые государственного технического университета (МАДИ) провели специальные и обстоятельные исследования «вадовской» ровности по различным критериям, как регламентированным ГОСТ 30412-96 «Дороги автомобильные и аэродромы. Методы измерения неровностей оснований и покрытий» и СНиП 3.06.03–85 «Автомобильные дороги» (просветы под 3-метровой рейкой и разность вертикальных отметок при шаге замера 5 м, 10 м и 20 м или попросту шаговая ровность), так и дополнительным, в том числе по международному индексу ровности IRI (International Raughness Index). Согласно международными нормам ровность оценивается следующим образом:
- IRI < 1,0 – отличное
- 1,0 ≤ IRI ≤ 1,5 – очень хорошее
- 1,5 ≤ IRI ≤ 2,5 – хорошее
- 2,5 ≤ IRI ≤ 3,5 – среднее
- 3,5 ≤ IRI ≤ 4,5 – удовлетворительное
- IRI > 4,5 – плохое
Каждая из зарубежных стран устанавливает свои национальные требования по допустимым (предельным) значениям неровностей нового покрытия по методу IRI. К примеру, в соседней Финляндии верхние слои разных категорий дорог не должны иметь неровностей больше 1,4–1,6 мм/м (IRI ≤ 1,4 ≤ 1,6), а нижние слои – больше 1,7–1,9 мм/м (IRI ≤ 1,7 ≤ 1,9). При больших значениях IRI покрытия в эксплуатацию могут не приниматься.
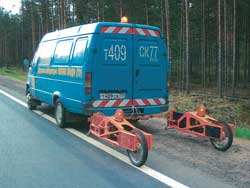
Рис. 2. Дорожная лаборатория МАДИ с двумя ДПП в рабочем положении.
Для тестирования микропрофилей поверхности автомобильной дороги использовалась передвижная лаборатория конструкции МАДИ (рис. 2), главным измерительным инструментом которой является запатентованный динамический преобразователь профиля (ДПП) с соответствующими блоками питания, регистрации, памяти и электронной обработки информации. Два типа похожих лабораторий с аналогичным принципом устройства и измерения неровностей действуют во Франции.
Объектом метрологического контроля и исследований МАДИ был участок км 110 – км 150 федеральной автомобильной дороги «Кола» Санкт-Петербург – Петрозаводск – Мурманск, причем участок км 110 – км 132 был полностью сдан в эксплуатацию после капитального ремонта в 2003 г,, а участок км 132 – км 150 на момент исследования (май 2004 г.) находился в работе, и на нем были уложены выравнивающий и нижний слои покрытия.
Результаты исследования показали, что по российскому нормативному значению просветов под 3-метровой рейкой на участке км 110 – км 132 с уложенным верхним слоем дорога полностью отвечает требованиям СНиП с вероятностью непревышения просветов 3 и 6 мм соответственно 99,4 и 100 %.
По нормативным значениям разности вертикальных отметок при шаге замера 5 м, 10 м и 20 м требования СНиП тоже полностью выполнены, причем вероятность непревышения этих нормативных значений составила в среднем 99,7 % (шаг замера 5 м), 98 % (шаг 10 м) и 98,3 % (шаг 20 м).
Оценка ровности покрытия на этом же сданном участке дороги (км 110 – км 132) по международному показателю IRI оказалась отличной, так как 0,52 ≤ IRI ≤ 0,88, или в среднем 0,72 мм/м.
Полученная статистика просветов под 3-метровой рейкой на поверхности уже нижнего слоя покрытия (км 132 – км 150) показала, что на всем протяжении обследования нормы СНиП тоже полностью выполнены, т.е. просветы ≤ 3 мм. При этом вероятность непревышения нормативного просвета 3 мм превосходит требуемое значение, равное 98 %. Поэтому состояние поверхности нижнего слоя по ровности специалисты МАДИ оценили на «отлично». Очевидно в этом, т.е. в тщательной подготовке нижележащей поверхности, и кроется секрет высокой ровности последующего верхнего слоя покрытия.
Правда, результаты определения разностей вертикальных отметок ординат микропрофиля поверхности этого нижнего слоя при шаге замера 5 м, 10 м, 20 м дали основание ученым МАДИ признать его ровность лишь хорошей с высказанным предположением, что последующая укладка верхнего слоя заметно поправит показатель ровности по этому критерию, что в дальнейшем и подтвердилось (табл. 1).
Таблица 1. Ровность покрытий крупных объектов ЗАО «ВАД» в 2003–2004 гг.
|
* Нижний слой устроен другим подрядчиком 1-2 года ранее
По международному индексу IRI, в среднем составляющему по нижнему слою 1,33 мм/м (реальный диапазон 1,15 ≤ IRI ≤ 1,65), ровность была оценена тоже на «хорошо».
Таким образом, «анатомия» показателей ровности нижних и верхних слоев покрытия на участке км 110 – км 150 автодороги «Кола» по различным критериям (по толчкомеру ТХК-2 на УАЗе неровности верхнего слоя в итоге составили 9 и 8 см/км) подтвердила правильность подходов ЗАО ВАД и избранных путей обеспечения высокого качества автомобильных дорог по ровности.
Вообще, ровность дороги или ее покрытия зависит от множества причин и факторов, и поэтому иногда не так-то просто и легко добиться высоких ее показателей. Достаточно указать, что «виновниками» появления на покрытии неровностей с «короткими волнами» (мелкие неровности) могут быть 13 причин, а с «длинными волнами» (более крупные и протяженные неровности) – 18 причин.
Обобщенно все эти и другие причины можно представить в виде более крупных 6 групп, каждая из которых отдельно отражает влияние на ровность самого материала, машины или технологической операции:
- Подготовка и состояние основания под укладку асфальтобетонных слоев.
- Состав и состояние асфальтобетонной смеси.
- Особенности доставки смеси на укладку и ее загрузки в бункер укладчика.
- Техническое состояние, правильная настройка и режим работы отдельных механизмов, рабочих органов и в целом самого укладчика.
- Несовершенный тип, плохая настройка или не очень точная и стабильная работа копирной лыжи и автоматической системы укладчика по поддерживанию поперечных уклонов и ровного продольного профиля укладываемого покрытия.
- Неправильная или «корявая» работа дорожных катков за укладчиком, способных существенным образом ухудшить или даже вообще испортить ровность хорошо устроенного укладчиком покрытия.
Большая часть из указанных причин и условий появления неровностей на поверхности покрытия с рекомендациями по их устранению довольно подробно и обстоятельно рассмотрена в статье «Практические проблемы устройства асфальтобетонных покрытий с высокой ровностью» (ежегодный каталог-справочник «Дорожная техника и технология», 2003 г.) и в некоторых других публикациях каталогов-справочников за 2000–2004 гг.
Однако два последних вопроса, или аспекта, из приведенного перечня, связанные с настройкой и работой копирной лыжи с автоматикой и дорожных катков, оказались плохо или мало освещенными. Во всяком случае, с точки зрения важности и степени их влияния на итоговую ровность строящегося покрытия, а также необходимых мер по нейтрализации основных негативных причин и факторов.
Сейчас уже трудно себе представить современный асфальтоукладчик без автоматической системы управления (АСУ) и поддержания заданного поперечного уклона и ровности продольного профиля покрытия дороги. А каких-то еще лет 40–45 назад функцию этой автоматики выполняли два оператора (слева и справа) выглаживающей плиты, осуществлявшие на глазок ход и величину изменения уклона и ровности, корректируя вручную угол атаки этой плиты и поперечное ее положение. Такой ручной «автоматике» соответствовал и не очень высокий уровень ровности покрытия.
Затем, после внедрения гидравлики на строительных и дорожных машинах, а на укладке асфальтобетона – копирных струн и лыж, появилась возможность процесс управления рабочей плитой укладчика и качеством устройства покрытий перевести в автоматический режим. В результате чего показатели ровности дорог заметно улучшились.
В действующем до сих пор СНиП 3.06.03-85 еще можно обнаружить следы реалий 25-летней давности, когда российские дорожники, не имевшие в достатке укладчиков с автоматикой, могли сдавать заказчику свои объекты по одним нормативам ровности покрытия, а обладающие такими укладчиками по другим, более жестким нормам. Сейчас это кажется странным, но эта реальность продолжает существовать и в 21-м веке.
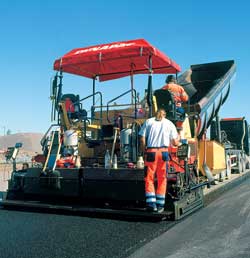
Смысл работы АСУ укладчика со струной или лыжей состоит в том, что в качестве базовой поверхности, от которой должна работать АСУ, не может быть принята реальная поверхность нижележащего основания с ее возможными буграми, впадинами и волнами. Для этого нужна либо ровно и туго натянутая по нивелиру бесконечная струна, либо длинная жесткая лыжа, скользящая по основанию совместно с перемещением укладчика и нивелирующая, т.е. сглаживающая, бугры и впадины до более ровного продольного профиля поверхности будущего слоя покрытия.
За вертикальным положением линии профиля (или лыжи) следит щуповый датчик автоматики, опирающийся на струну или лыжу и посылающий соответствующие сигналы в блок сравнения (аналогий), из которого поступают управляющие команды в гидравлическую систему гидроцилиндров подъема или опускания шарнирной точки крепления продольных брусьев (лонжеронов) рабочей плиты, т.е. на изменение угла атаки рабочей плиты, и таким образом, на корректировку толщины укладываемого слоя асфальтобетона.
Следует обратить внимание на два важных обстоятельства. Во-первых, на длину лыжи, минимальное значение которой должно быть увязано с амплитудами (глубина, высота) и длинами волн неровностей на основании. Чем «корявее» основание, тем длиннее должна быть лыжа. В самом худшем случае этих показателей основания идеальной может стать бесконечная ровно натянутая струна (самый оптимальный аналог лыжи).
А вообще существует правило – чем длиннее лыжа, тем ровнее покрытие. ЗАО ВАД почти на всех своих укладчиках использует длинномерные (до 18–24 м) двойные лыжи по типу французской, реализуя при этом высокую ровность.
Во-вторых, совместная работа автоматики и гидравлики укладчика будет безупречной в том случае, когда время импульсных сигналов и команд автоматики будут соответствовать необходимому времени срабатывания гидроцилиндров, регулирующих угол атаки рабочей плиты.
Любая гидравлическая система дорожной машины, в том числе и асфальтоукладчика, имеет вполне конкретные свои показатели и параметры (рабочее давление, величину и скорость потока гидравлической жидкости, габариты гидроцилиндров, диаметры шлангов и труб и др.), которые и определяют необходимый первоначальный силовой момент (величина давления и продолжительность его действия) для того, чтобы своевременно и плавно переместить шток гидроцилиндра вверх или вниз на требуемую величину.
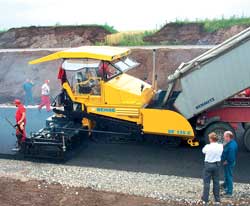
Сам силовой момент создается жидкостью от работающего гидронасоса, поступающей в гидроцилиндр через электрически управляемый электромагнитный клапан. Время действия электрического сигнала по команде электронной системы управления (импульс автоматики) должно быть равно времени работы электромагнитного клапана. Минимальное время импульса автоматики должно соответствовать минимальному моменту для начала срабатывания (перемещения) штока гидроцилиндра. Если импульс автоматики окажется недостаточным, движение штока будет «ленивым» (замедленным). Наоборот, при очень большом импульсе движения штока будут резкими и, может быть, даже чрезмерными по величине.
Поэтому требуется подбор и четкое согласование величины (продолжительности) электрического импульса электронной системы со временем необходимого импульса для конкретной гидравлической системы укладчика. На разных моделях и типах последних это время может составлять значения в диапазоне от 10 до 100 мсек (0,010–0,100 сек). Например, на укладчиках Dynapac оно близко к 100 мсек, Vögel комплектует свои последние укладчики автоматикой с 60 мсек, а на некоторых укладчиках Титан фирмы Ingersoll Rand-ABG (IR-ABG), которые комплектуются автоматикой фирмы MOBA Mobile Automation, такое время может составлять 35–50 мсек.
При отсутствии указанного согласования автоматика работает плохо, не обеспечивая ожидаемой ровности покрытия. Поэтому аналоговые электронные приборы создаются с различным временем импульса и тщательно подбираются под конкретный экземпляр укладчика. Современные же цифровые приборы можно регулировать и подстраивать на необходимую продолжительность импульса. В этом их преимущество перед аналоговыми приборами. На все на это следует обращать внимание экипажа асфальтоукладчика, в противном случае автоматика и гидравлика будут срабатывать несвоевременно и порождать неровности на покрытии.
В последнее время фирмы, причастные к разработке и выпуску автоматических систем управления рабочими органами дорожных машин (асфальтоукладчики, холодные планировочные фрезы, автогрейдеры, бульдозеры), стали проявлять заметную активность в своих усилиях по созданию новых, более совершенных типов таких систем. Обусловлено это возросшими требованиями государственных и иных заказчиков к качеству возводимых дорожных сооружений. В Европе и США успешно и давно действует принцип гарантийных обязательств подрядчика перед заказчиком. В Азии тоже расширяется использование этого принципа. А в ряде стран (Испания, Франция, Ирландия и др.) окончательную оплату работ за построенную дорогу связывают непосредственно с ее качеством. Чем выше качество, тем более высокая плата. Поэтому все технологические новинки, работающие на качество, находят позитивное отношение у их потребителей.
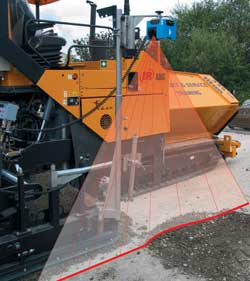
Рис. 3.Асфальтоукладчик Titan с лазерной Road Scaner Sistem (фирма IR-ABG.)
И неудивительно, что теперь появились первые автоматические системы управления лазерного типа, давно уже привлекшие внимание и породившие определенные ожидания и надежды дорожных специалистов. Американо-немецкая фирма IR-ABG стала распространять информацию и рекламные проспекты об оснащении укладчиков Титан бесконтактной Road Scaner Sistem лазерного типа (рис. 3), имеющей, по утверждению фирмы, ряд достоинств и преимуществ перед существующими системами.
Такая новая по существу лазерная лыжа длиной 12 м (6 м перед сканером и 6 м после него) легко и быстро монтируется на укладчике, не создавая помех и неудобств в работе или транспортировке укладчика. Очевидно, все плюсы, минусы и особенности такой системы прояснятся в ближайшем будущем, когда будет накоплен первичный практический опыт ее применения.А пока более широко «в реальное дело» за последние 5 лет пошли ультразвуковые АСУ, которыми, как само собой разумеющейся реальностью, стали комплектоваться асфальтоукладчики ряда американских, японских и европейских фирм. Бурно развивающаяся в последнее время дорожная отрасль Китая стала закупать почти до 500 таких систем в год.
Известная фирма Vögel разработала свою собственную ультразвуковую автоматическую систему Niveltronic для оснащения своих укладчиков (рис. 4), американские укладчики Cedarapids комплектуются системой Topcon Paver Sistem с подвесной на укладчике бесконтактной лыжей Smoothtrac длиной 9 м, на которой с равным шагом закрепляются 4 ультразвуковых датчика контроля продольного профиля покрытия, фирма IR-ABG свои укладчики продолжает оснащать ультразвуковой системой фирмы MOBA.
![]() |
Рис. 4. Асфальтоукладчик фирмы Vögel, оснащенный ультразвуковой системой Niveltronic |
Как уже отмечалось, большинство имеющихся сегодня у дорожников асфальтоукладчиков оснащены АСУ, работающими по принципу механического контактного копирования основания, неровности которого в уменьшенном или сглаженном виде воспроизводятся на поверхности вновь укладываемого покрытия.
![]() |
Рис. 5. Схема различий между обычным одинарным ультразвуковым датчиком и пакетным «Sonic Ski» фирмы МОВА |
Фирма MOBA обратила на это особое внимание и пришла к выводу, что избежать этого можно, если одновременно нивелировать или бесконтактно контролировать основание в нескольких точках и результат нивелировки всех таких точек усреднять. Этот принцип был запатентован и реализован в ультразвуковом пакетном или групповом датчике «Sonic Ski» (рис. 5), в котором, в отличие от других известных ультразвуковых датчиков с одной точкой нивелировки, на продольном отрезке основания длиной 25–30 см производится измерение высотного положения 5 точек, причем самый большой и самый маленький результаты отбрасываются, а остальные три усредняются. Это позволяет исключить единичные не характерные отклонения или случайные препятствия на основании (нога, камень, инструмент и т.п.), оказавшиеся под датчиком, и свести на нет возможные неточности и огрехи. В итоге должна возрасти ровность устраиваемого покрытия.
Однако этого фирме MOBA показалось мало, и она пошла еще дальше, предложив комбинацию нескольких датчиков «Sonic Ski» разместить вдоль асфальтоукладчика и увеличить тем самым длину полосы сканирования. В частности, на легкой дюралевой балке длиной 12 м, жестко закрепляемой на тяговых брусьях (лонжеронах) укладчика, фирма МОВА устанавливает три датчика «Sonic Ski», получив новую измерительную систему под названием «Big Sonic Ski» (рис. 6) с большей длиной ультразвукового контроля основания, на которой действует тот же принцип усреднения, что и в «Sonic Ski».
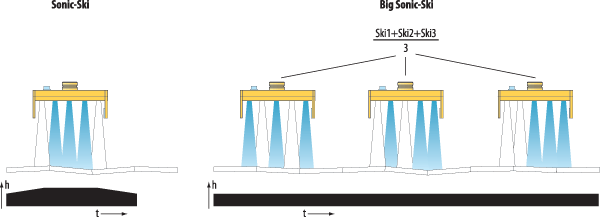
Рис. 6. Схема различий в управлении ровностью укладываемого покрытия системами ультразвуковых датчиков «Big Sonic Ski» и «Sonic Ski»
За счет такого способа измерения, сортировки и усреднения значений неровностей основания даже растянутые или продолжительные волны, впадины и выпуклости квалифицируются системой автоматики как ошибки и исключаются из показателей измерений или же попадают в общий усредненный результат в незначительном процентном соотношении. Поэтому ровность покрытия, уложенного 12-метровой лыжей с «Big Sonic Ski» не должна уступать ровности после даже 18- или 24-метровой лыжи, осуществляющей контактное механическое копирование основания, при котором учитываются только самые высокие выступающие точки его поверхности (бугры, вершины волн и т.п.) и при котором не производится усреднения итоговых показателей измерений.
Дополнительным для дорожного подрядчика и важным вообще для асфальтобетонной технологии преимуществом акустической АСУ, по мнению специалистов фирмы МОВА, может оказаться возможная экономия средств и времени, так как для таких новых систем в ряде случаев может стать совсем необязательной стопроцентно хорошая, тщательно и заранее подготовленная базовая поверхность слежения (копирования, нивелировки, сканирования) в виде, например, предварительно уложенного выравнивающего слоя или искусственно натянутой струны, как это рекомендовалось, а иногда и требовалось делать для прежних АСУ с контактной лыжей. Очень заманчивая перспектива, правда, требующая специальной практической проверки.
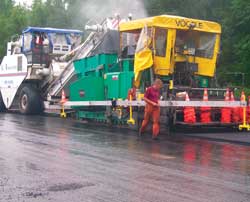
Рис. 7. Укладка асфальтобетонного покрытия на автодороге А114 асфальтоукладчиком Vögele Super 2500, оснащенного ультразвуковой лыжей фирмы MOBA, при участии перегрузчика Shuttle Buggy фирмы Roadtec.
В строительный же сезон 2004 г. ЗАО «ВАД» совместно с ООО «СДМ-БАЛТ» провело широкие сравнительные испытания 12-метровой акустической лыжи с датчиками «Big Sonic Ski», любезно предоставленной, смонтированной на асфальтоукладчик Vögel Super 2500 и настроенной фирмой МОВА (рис. 7).
Испытания проводились на укладке нижних и верхних слоев асфальтобетонного покрытия на 30-километровом участке капитального ремонта федеральной автомобильной дороги А114 Вологда–Новая Ладога (между Сомино и Пикалево в Ленинградской обл.).
В условиях непрекращающегося движения транспорта укладка слоев покрытия шириной 8 м выполнялась поочередно двумя полосами по 4 м. Одна из них устраивалась с участием имеющейся на укладчике длинномерной (18–24 м) двойной лыжи по типу французской и автоматики Vögel, а другая параллельная – с помощью лыжи и автоматики МОВА.
Что же показали испытания ультразвуковой лыжи МОВА. Во-первых, при устройстве нижних слоев покрытия, которое производилось на предварительно уложенный выравнивающий слой, лыжа и автоматика МОВА обеспечили лучшие показатели ровности по сравнению с длиномерной лыжей в среднем на 5 см/км по ТХК-2 на автомобиле ГАЗель, хотя на отдельных участках это положительное различие доходило до 17–19 см/км при общих средних показателях ровности нижнего слоя по всем 30 км 61 (длинномерная лыжа по типу французской) и 56 см/км (ультразвуковая лыжа МОВА).
Во-вторых, ровность верхнего слоя с использованием лыжи МОВА на укладчике Vögel Super 2500 тоже оказалась в среднем на 4–5 см/км лучше ровности под длиномерной лыжей (на 19 из 22 км протестированных, или на 86 %). Правда, когда на части участков укладку верхнего слоя выполнял укладчик Титан 325ЕРМ с обеими лыжами, то разница между ними сократилась в среднем до 2 см/км, но опять же в пользу МОВА. Различие не столь существенное, но следует помнить, что лыжа МОВА в 1,5–2 раза короче конкурентки. Очевидно, у последней выравнивающая способность (отклонение ровности нижнего слоя к ровности верхнего) оказалась ниже (≈2,85 раза), чем у лыжи МОВА (≈3,05 раза).
По итогам испытаний и полученных общих показателей ровности участка этой дороги, в том числе по международным нормам и оценкам IRI (см. табл. 1), ЗАО ВАД приобрело комплект ультразвуковой лыжи и автоматики МОВА.
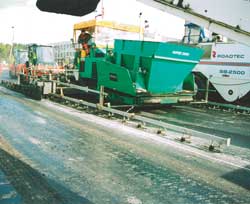
Устройство асфальтобетонного покрытия ЗАО «ВАД» с использованием длинномерных, многоопорных лыж по типу французких.
В технологии асфальтобетонных работ устройство дорожного покрытия, в том числе с высокой ровностью, завершается операцией уплотнения, которую выполняют различного рода самоходные катки, специально создаваемые для этих целей. То, что сами катки, их типы и приемы выполнения ими операции укатки влияют в той или иной степени на ровность покрытия, известно давно и многим.
Конечно, есть хорошо знакомые общие требования и правила ведения укатки асфальтобетона в покрытии на дороге – обеспечивать плавность реверса хода катка, во время реверса хода отключать вибрацию, не допускать остановок на укатываемой полосе, повороты, смещения с полосы на полосу и другие маневры производить только на уже уплотненной и заметно остывшей части покрытия, начинать уплотнение следует с крайних полос, постепенно смещаясь к середине покрытия и т.д. и т.п. Их соблюдение, как правило, способствует улучшению ровности или, во всяком случае, не ухудшает ее.
Однако есть и другие особенности этой операции, оказывающие порой более значительное влияние на ровность, и они должны учитываться не только машинистами катков, но и мастерами, прорабами и технологами.
Самый большой вред ровности хорошо устроенного укладчиком покрытия может нанести неправильный, бездумный или безграмотный выбор статического или вибрационного катка по его весовым и вибрационным параметрам. Создаваемые их вальцами давления на контакте с уплотняемым слоем вызывают соответствующую деформацию или осадку этого слоя. Если эти контактные давления чрезмерны, осадка слоя тоже будет большой, причем иногда настолько, что асфальтобетонная смесь начинает выдавливаться из-под вальца, образуя впереди него так называемую сдвиговую волну.
Эта даже незначительная, а порой и не очень заметная волна нежелательна, так как она является источником или причиной будущих неровностей на покрытии. К тому же на ее гребне могут возникать видимые и невидимые поверхностные трещины. Сначала неглубокие (2–3 мм), а по мере укатки проникающие все глубже и глубже.
Такие трещины появляются вследствие того, что асфальтобетон имеет предел прочности на растяжение в 3–4 раза ниже, чем на сжатие. А на гребне сдвиговой волны как раз и происходит растяжение материала. Поэтому в фирме ВАД заведены два правила или требования для неукоснительного исполнения. Во-первых, перед включением вибрационного режима уплотнения сразу за укладчиком виброкаток должен выполнить 2–3 прохода в статическом режиме, чтобы произвести некоторое предварительное подуплотнение и упрочнение горячей смеси своими сравнительно незначительными контактными давлениями в статике и снизить тем самым величину сдвиговой волны при последующем включении вибрации.
Во-вторых, перемещение виброкатка с включенным вибратором должно идти только от укладчика, а его движение к укладчику необходимо выполнять без вибрации. Такой технологический прием снижает нагон сдвиговой волны при ее перемещении вместе с катком с более горячей смеси в сторону более остывшей.
Кстати, при малых контактных давлениях вальцов статических и вибрационных катков ровность получается вполне приемлемой, но ухудшается качество уплотнения покрытия. Если же они «солидные» и превышают прочностные показатели укатываемого асфальтобетона, страдает не только ровность, но и опять же качество уплотнения.
Поэтому подбор катков следует производить по оптимальному (должно быть ни много, ни мало) значению индекса контактных давлений с учетом толщины уплотняемого слоя и состояния асфальтобетонной смеси по плотности и температуре на каждой стадии укатки. Методология такого подбора изложена в настоящем каталоге-справочнике в статье «Новая усовершенствованная технология устойчиво обеспечивает высокое качество уплотнения асфальтобетона».
Способствуют снижению неровностей на покрытии размеры вальцов катка, и в первую очередь их диаметры, а также правильное назначение рабочей скорости укатки покрытия с вибрацией. Чем больше диаметры вальцов, тем ровнее получается покрытие из-под катка с такими вальцами. Если есть реальные виброкатки, например, с шириной вальцов 1680 мм и диаметрами 1140 (HD75, HD 075V), 1200 (DV8) и 1300 мм (СС422, СС422HF), то предпочтение, при одинаковых или близких индексах контактных давлений, следует отдавать катку с вальцами 1300 мм.
На современных асфальтобетонных виброкатках используемая частота колебаний вальца различна и может иметь одно из значений диапазона 40–70 Гц. Для получения надлежащей ровности и реализации требуемого качества уплотнения покрытия желательно, чтобы вибрирующий валец за один проход виброкатка совершил от 2 до 4 или в среднем 3 цикла нагружений по любой точке укатываемой поверхности. Как утверждают американские дорожные специалисты, нужны 35–40 циклов нагружений на 1 м пути катка.
Отсюда следует, что максимальная рабочая скорость виброкатка при 40 и 70 Гц должна быть различной. В противном случае, особенно на больших скоростях катка с низкой частотой колебаний вальца, на покрытии могут появиться и быть даже видимыми после дождя или в свете ночных фар автомобиля мелкие волнообразные неровности.
И еще об одной разновидности неровностей дорожного покрытия. Речь идет о продольных и поперечных швах соединений двух полос покрытия, устраиваемых с разрывом во времени. Эти так называемые холодные швы, особенно продольные, очень часто и быстро разрушаются, образуя на покрытии неровности в виде трещин, обломов, выбоин и даже ям.
Чтобы этого не происходило и не возникали дискуссии и трения с заказчиком по поводу нежелательности выполнения асфальтобетонных работ с холодным швом, ЗАО «ВАД» для себя и для заказчиков решило эту проблему технологическим путем раз и навсегда. Теперь все холодные швы стоят в эксплуатации ровно столько, сколько прочно стоит само покрытие дороги.
Специфика технологии устройства холодного шва состоит в том, что для уплотнения горячей смеси у такого шва и прочной его спайки выделяется отдельный гладковальцовый виброкаток, который особым способом (схема на рис. 8) постепенно или поэтапно выполняет эту операцию, исключающую боковой сдвиг горячей смеси в сторону от шва. Этим и достигается высокая плотность смеси у шва и прочность самого контакта. Хорошим и полезным помощником, дополняющим такую технологию, в ЗАО «ВАД» служит малогабаритный газовый разогреватель холодного шва инфракрасного типа фирмы Abacus (ФРГ).
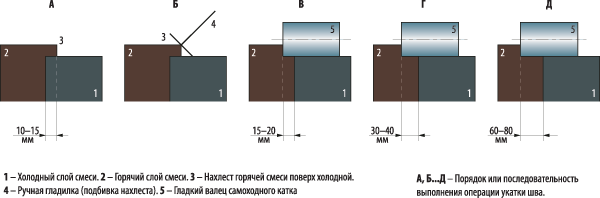
Рис. 8. Технологическая схема уплотнения горячего асфальтобетона на стыке холодного шва специально выделенным катком.
И, наконец, последнее. Ровность и плотность покрытия могут существенно пострадать при его укатке, если сцепление укладываемого верхнего слоя с нижним основанием слабое или недостаточное из-за плохой подгрунтовки, наличия водяной прослойки или мусора. Это обуславливает излишнюю горизонтальную подвижность уплотняемого слоя, особенно катками с большими статическими и динамическими контактными давлениями, и ухудшает ровность его поверхности.
Прочность с устойчивостью отдельных слоев дороги и продолжительная ровность ее покрытия взаимосвязаны. Кто хочет строить дороги с высокой долговременной ровностью и большими сроками своих гарантий, тот должен не только уметь укладывать такие слои ровно, но и грамотно и эффективно выполнять уплотнение земляного полотна, щебеночного основания и асфальтобетонного покрытия.